Manufacturers must consider and control many factors to ensure an accurate, reliable leak test. Factors that can affect your leak test include test design, part design, air quality, environment, and temperature.
Temperature is a very important factor in ensuring the accuracy and reliability of your leak test and it can affect your test in ways you may not realize, including:
- Part/fixture temperature
- Test air temperature
- Environmental temperature
When leak testing, the part, test air/gas, fixture, and environment around the machine need to be the same temperature. If one of them is different, there will be a temperature change while the part is getting tested which will impact the accuracy of the test result.
A temperature change of even 1°C leads to several 100 Pa pressure change within the measurement phase, which can drastically alter your test results. That pressure change will be inaccurately measured as a leak (or cover up an actual leak).
Read on to learn how to avoid inaccurate leak test results by controlling the ways temperature can affect your leak test.
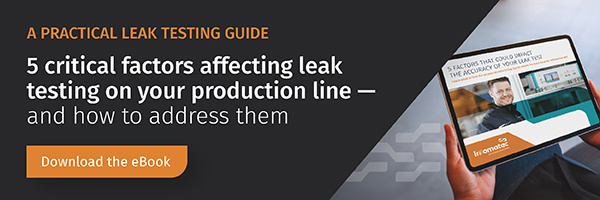
Part and fixture temperature
If the part being leak tested has a different temperature than the environment of the test station, it will have a considerable effect on the test result. The most common reason for a part to be a different temperature than the fixture and/or surrounding environment is if the part was subjected to heat-transferring process(es) before arriving at the leak test station. Manufacturing processes that can cause heat-transfer include washing, welding, soldering, spraying (plastics), and more.
Thankfully, there are a variety of ways to compensate for temperature when designing your leak test, including adding longer stabilization times to the test to allow for the part to cool down before the leak test measurement, or choosing to use a heat-resistant leak test method, such as tracer gas leak testing.
Test air temperature in leak testing
The temperature of pressurized air used for leak testing must be the same temperature as the part under test and the fixture. This can be controlled in a variety of ways depending on the test scenario, including installing a heat exchanger on the air leak tester.
There is also the issue of compression heat, which happens when filling a test specimen with test air. During this process, the existing atmospheric air in the test specimen is compressed (also called the "air pump effect"). This compression raises the temperature of the material in the test specimen. The heated compressed air then cools as it mixes with the filled test air and releases its heat to the test piece housing. This causes a pressure drop to occur immediately after filling, which could be recorded as a false leak.
To compensate for this and ensure an accurate leak measurement, the test must provide adequate stabilization time before the leak measurement takes place. If the target cycle time doesn’t allow for adequate stabilization time, manufacturers could consider tracer gas leak testing methods instead of air leak testing.

Environmental temperature
Environmental conditions in a factory can have a drastic effect on the accuracy of a leak test. It is best to analyze the production area before building a leak test machine to take note of any conditions that could impact the leak test and develop the machine design accordingly. Environmental conditions that could impact the accuracy of your leak test include:
- Indoor/outdoor temperature and humidity (which can change based on season, etc.)
- Direct sunlight through large windows
- Indoor HVAC settings (which can change based on season, etc.)
- Air drafts through doors or gates into the test area
- Other heat sources that may be present on the plant floor, like hot machinery, industrial vehicles, etc.
Other ways to manage temperature during leak testing
While we have discussed ways to control and manage the effects of temperature in the specific examples above, the below options can also be considered in some instances:
- Set a delta (D) temperature which the test cannot exceed (causing the test to stop)
- Use a temperature compensation calculation—though this is only advisable under very specific circumstances, with the the oversight of a measurement engineer to ensure accuracy
Are you having trouble achieving an accurate, reliable leak test? Contact the leak test experts at innomatec!
WANT TO LEARN MORE ABOUT DESIGNING AN ACCURATE LEAK TEST?
DOWNLOAD EBOOK: 5 FACTORS THAT IMPACT THE ACCURACY OF YOUR LEAK TEST
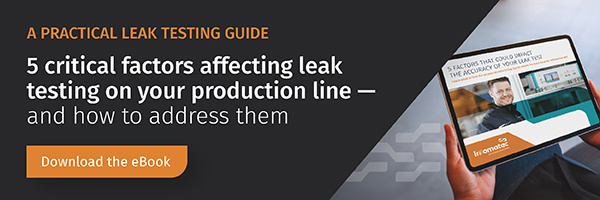