An accurate, reliable leak test relies on good test design. Factors including the test bench, test fixturing, and sealing must work together to deliver an accurate measurement and avoid false leaks or false passes.
Once you have identified the best leak test method for your part, you will design your test, taking into consideration the sealing, pressure, fixturing, environment, and process. Learn more about each of these factors below.
Test seals
The quality and location of connectors and seal(s) can make a huge difference in the accuracy of a leak test. You need a tight, well-fit seal, placed as close to the original sealing line as possible. Though could be certain cases where it is best to place a sealing line directly on the sealing joint of the part, it is generally best practice to leave a small distance between the sealed location on the part and the test seal to make sure that the machine seal does not accidentally cover up a leak.
Test pressure
When it comes to the design and setup of test seals, pressure is also very important to consider. If too much pressure, or force, is applied when the fixture presses the seal into place, this could compress the part, resulting in damages to your part and missed leaks. Your test must be designed to only apply the amount of force necessary for a tight seal.
Test fixturing
Proper fixture design is what keeps a part stable during the test process, which is important for an accurate leak measurement. This becomes particularly important if you are using high test pressure, as the force exerted on the part and fixturing could cause it to bend, expand, or be damaged during test. Fixture design must take into consideration the material and size of the parts or assemblies being tested to control and mitigate any expansion or contraction that could impact the reliability of the leak test measurements.
Test floor environment
The environment around your leak test station can have a drastic impact on leak test results. Factors such as HVAC units and air drafts, direct sunlight or heat sources, vibrations, and active machinery on the plant floor must be considered in the design of your leak test to mitigate any affects that temperature, ambient pressure, and movement could have on your leak test measurements.
Other test processes on the line
Manufacturers sometimes overlook how operations happening further up the line could have an impact on the results at the leak test station. Operations including those that creating heat, a wet surface, or debris could affect the accuracy of your leak test. This may require designing your leak test to allow for longer stabilization times so the part can cool down before the leak test measurement, or changing the test method to a heat resistant method like tracer gas method, etc.
Need help designing a leak test?
innomatec has over 40 years’ experience helping top manufacturers across the globe design and improve their leak tests for the most accurate, reliable results. innomatec engineers will work with your team to review your part design, analyze the production area and environment, and conduct laboratory tests before advising on the ideal leak test design for your part or assembly. Contact us today to discuss your leak test!
WANT TO LEARN MORE ABOUT DESIGNING AN ACCURATE LEAK TEST?
DOWNLOAD EBOOK: 5 FACTORS THAT IMPACT THE ACCURACY OF YOUR LEAK TEST
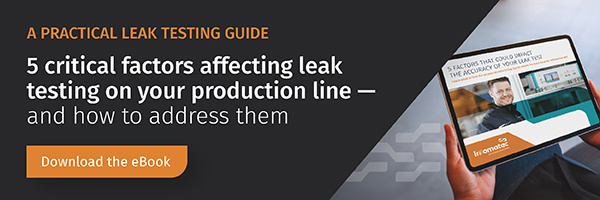