In our last post, we discussed how leak test design factors including test bench design, and test fixturing and sealing solutions must be considered in order to achieve an accurate leak test measurement. Part design is also an important consideration in achieving a reliable, repeatable leak test.
Different aspects of part design, including size, materials, and part stability will impact the way a part or component needs to be tested. Learn more about the different aspects of part design below and how to overcome these challenges to achieve the most accurate leak test results and deliver reliable product quality.
Part size
Problem: When using air leak test methods to test large volume parts, the measurement is highly sensitive to shifts in pressure and temperature. This can drastically affect the accuracy and repeatability of the results. Small parts may also be impacted, depending on factors such as test pressure and material composition.
Solution: To overcome this, the leak test must be carefully designed to control test pressure, counteract any thermal effects that may be present, and ensure proper stabilization before test. Manufacturers can also optimize fixturing closer to the part and/or add filler blocks to reduce the internal test volume as much as possible.
Part materials
Problem: It can be more difficult to achieve reliable, repeatable measurements when testing parts and components made from porous materials, like cast housings, along with designs that incorporate porous bonding, gap filler materials, and flame reduction foams, etc. This is due to their ability to absorb heat and pressure, both of which can affect test accuracy.
Solution: To remedy this, the test must be designed to properly control for these factors, which could include paying extra attention to test pressure, stabilization time, testing different measuring solutions and compensations, and more.
Part stability
Problem: Along with the instability of porous or absorbent materials, assemblies with flexible components or parts made from thin or flexible materials are also susceptible to expansion when air pressure is applied. This can cause inaccurate pressure loss readings, and more, leading to inaccurate pass/fail results.
Solution: To remedy this, the test method, test pressure, and fixturing must be carefully considered during the test design phase to prevent issues related to part stability from impacting your leak test results. There are many different solutions to stabilize parts during a leak test, which can be discussed based on the specifics of the application and test part.
How small alterations to part design could provide a better, more cost-effective leak test
While the different components of test design, including test method, test pressure, and fixturing, must be considered for an accurate, reliable leak test, it may also be worth considering whether changes to the part itself could make for a more reliable leak test. Sometimes even small alterations to a part can even deliver a faster cycle time and more cost-effective design.
Sometimes, a minor modification to a part or component can significantly simplify and reduce the cost of leak testing. Certain components are challenging to test for leaks; for instance, parts with hollow profiles can hinder the easy escape of tracer gas during testing. In such cases, if feasible, making a small, drilled hole or designed opening in the side of the profile can facilitate a much simpler and more reliable leak test.
During air leak testing, "nearly" leak-tight areas within the test part can lead to complications, as these areas or volumes may produce false leaks depending on the testing methods used. If possible, modifying the part design to completely seal these spaces can facilitate a simpler and more accurate leak test.
Need help designing a leak test?
innomatec has over 40 years’ experience assisting leading manufacturers worldwide in designing and enhancing their leak tests for optimal accuracy and reliability. We are uniquely equipped with in-house expertise and capabilities to meet any leak test requirement, offering industry-leading instrumentation for all testing methods, pressure-tight connec® seals and connectors, as well as comprehensive design and development of leak test machines. Contact us to discuss your leak test today.
WANT TO LEARN MORE ABOUT DESIGNING AN ACCURATE LEAK TEST?
DOWNLOAD EBOOK: 5 FACTORS THAT IMPACT THE ACCURACY OF YOUR LEAK TEST
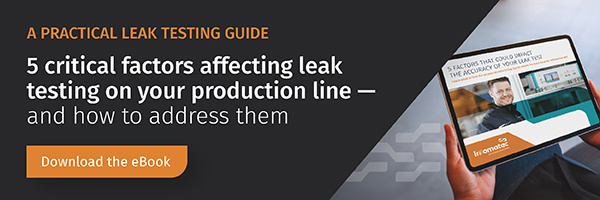