Hydrogen energy is an evolving industry with applications in transportation, industrial factory environments, and more. Due to the reactivity of hydrogen, leak detection is a very important part of the manufacturing process for these hydrogen components, such as hydrogen fuel cells, hydrogen tanks, and hydrogen refueling systems, pipes, valves, and more.
Hydrogen can be a very dangerous gas if it leaks, and it can leak through extremely small cracks, posing a challenge for leak testing. Even a small concentration of leaked hydrogen mixed with oxygen can make hydrogen flammable and explosive, making it of critical importance to ensure a precise and reliable leak test designed to detect even the smallest leaks during the manufacturing process.
How to leak test hydrogen components
Since the required leak rates for hydrogen components are so small (1 x 10-6 mbar*l/s or smaller), components that will have direct contact with hydrogen must be tested with tracer gas or helium leak testing methods. Air leak test methods are often not able to meet the low leak rates required for hydrogen component leak testing. Using the tracer gas leak test method, manufacturers could use helium, a helium mixture, or a forming gas mixture of hydrogen and nitrogen.
Manufacturers may think that since they are testing a hydrogen component that a hydrogen mixture would be the best gas to use for the leak test. However, there are many applications when testing hydrogen components where we would recommend helium instead.
Why use helium to test hydrogen components?
As the smallest atom in the periodic system, one could reason that hydrogen would be the best gas to identify the smallest leaks. However, the electron configuration of helium actually makes it “smaller” than hydrogen. And furthermore, hydrogen always comes in a pair (H2). This means that through the same leak opening, more helium atoms would leak out than hydrogen atoms, making it easier to identify the smallest leaks, and delivering a more accurate leak measurement.
Using helium can also boost the accuracy of your leak test
Testing your hydrogen components with helium also poses further benefits, contributing to higher accuracy of your leak test. This comes down to concentration and environment.
First, hydrogen can only be used at a maximum concentration of 10%, often mixed with nitrogen. If it is used at any higher concentration, it can cause reactions with common manufactured materials, including steel and aluminum, and pose health and safety risks. Helium, however, is a non-reactive element. It does not react with any materials, is not flammable, and does not pose any safety risks, thus it can be used at 100% concentration. This higher concentration allows for a quicker, more accurate leak test measurement and smaller leak rate measurements.
Second, hydrogen can be present in the background atmosphere of a manufacturing environment. For example, if the facility runs a natural gas furnace, or has forklifts or other machinery running on natural gas in the plant, these machines will produce hydrogen, releasing it into the plant atmosphere. High-humidity climates can also introduce hydrogen into the plant environment. When hydrogen is present in the test atmosphere, it can affect the background level of your test and impact the accuracy of your leak test results. You can avoid this potential issue by using helium.
Reliable leak test solutions for testing hydrogen components
As the use of hydrogen as an alternative energy continues to evolve, innomatec’s engineers are here to assist your team to ensure a safe, effective manufacturing environment. We will help you understand the testing requirements for your applications and ensure you have the most efficient system, including discussing options for helium recovery/recycling to reduce production costs and improve sustainability in your plant. Contact us today to discuss your leak test!
WANT TO LEARN MORE ABOUT DESIGNING AN ACCURATE LEAK TEST?
DOWNLOAD THE EBOOK: 5 FACTORS THAT IMPACT THE ACCURACY OF YOUR LEAK TEST
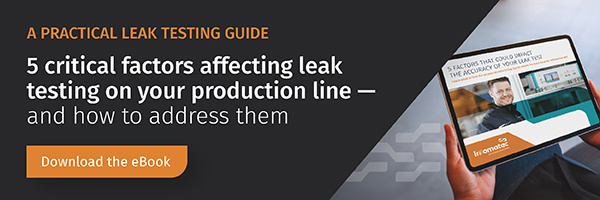